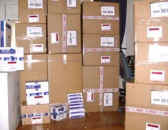
Shipments ready for pick-up...
|
Turntables are one of the more difficult audio components to pack for safe
transit. Having been a dealer for many brands of tables over the past
38+ years,
I know what works and what doesn’t. I have un-boxed many new tables that were
packed using “factory” packing. When tables are shipped from the manufacturer,
they are generally shipped with the platter and the dustcover removed and stored
in recesses, that are molded into their custom made Styrofoam packing, that was
designed by professionals that have researched what works and what doesn’t.
If the turntables original packing materials are available it
is probably best to use those. If the cosmetic quality of the original box is important,
then that box should be put into another box. Unless the original foam
packing is included with a table (and it rarely is) and is intact, custom and
sufficient / appropriate packing must then be made. While every turntable
presents a different packing challenge, there are some basic procedures that we
repeat and so far has resulted in almost flawless success. No system is
“fool-proof” (even factory packaging) and there are likely a few other
variations that will work equally well, maybe better, but not following these or
other appropriate procedures is likely a recipe for failure.
We typically ship large items
such as turntables via Fed Ex / FedEx or UPS ground (we use USPS / Post Office
/ Postal Service generally for smaller items).
Prior to the packing, the table is prepped for packing. If it is a
“single play” type table, the platter is removed. The platter can weigh
anywhere from a pound or two to as much as 10 or 20 lbs. As a “static” load
this isn’t too bad, but when being dropped from a stack of boxes,
a shelf in the delivery truck,
or even from a hand truck / dolly toppling over, a 4 lb platter can
pretty easily reach a weight in motion of 40 lbs. Much more weight than the
plinth and spindle / bearing were ever designed to handle. Leaving the platter
in place will generally result in a bent spindle,
distorted bearing, busted plinth
or a combination of these. We’ll talk about what is done with the platter and
rubber mat later. Next if there are any transport screws (not as common on
single play turntables as changers, but may still be used) they should be
installed /
engaged. Some single-play tables may have had transport screws, but they
were
usually removed for use and subsequently misplaced or
discardedt. Suitable replacements
should be obtained and installed unless other ways of stabilizing the suspension
are available such as the use of shims. On changer / stacker type tables or
tables that need their suspension secured, and if the locking screws are not
available, then 5” shrink film is used to secure the platter and / or suspension
in place (done with dust cover removed). Also on stacker type tables, the long
play spindle is removed if practical. If available the “short-play” spindle will be installed
prior to the shrink wrap operation as this is a great place to “store” it for
shipment. The long-play spindle will be bagged and packed safely on it’s own.
The tone-arm is then secured in place in it’s “locked” position with a
twist tie, painters tape or other
adequate means.
The counter-weight is either then removed and packed separately or
supported in place
by foam if it is not 'practically' removable. Many
styluses and dust-covers are damaged / destroyed by counter-weights flying
around inside that were not secured. Next the dust-cover is reinstalled if it
had been removed. A thin sheet of “poly-lam” foam is placed in
between the turntable base and the dust cover. Next the dust-cover is VERY FIRMLY secured in place with
stretch film from every direction. Once sealed down the turntable and
dustcover becomes a solid unit. No motion is allowed or loose
parts should be detected (we invert the table and shake it up and down to make
sure of that).
Next, our tables are usually,
housed in a
1.5" and 2" sheet foam "box"
(these are foam sheets made for house insulation and available at most home
improvement stores),
cut and assembled to fit exactly. Once the table is sealed and there are
no parts inside "rattling around" to break things or scratch the dust cover, the
foam 'box' is built around it.
On tables that have suspension built into the feet, small depressions need
to be "dug" in to the foam where the feet are, so that the tables weight is not
on the feet for shipping. The feet's own
internal suspension is not sufficient for this
protecting the unit in transit. Any "play" or
space inside the foam box, should be filled with foam
or bubble wrap. Typically there is room for a sheet of 1/2"
bubble wrap on the top. Then a top plate of 2", 'high-density'
(the expensive, pink type) foam is
sealed down tight to the rest of the foam box with the
stretch film. The platter and rubber mat are usually stretch filmed to the top of the
box taking care to make sure the mat is not bent or allowed to bend / wrinkle.
The best way to ensure this is to place the mat down first on the box, then
cover it with the platter positioned up-side down, to hold it in place.
If there are any protrusions from the back of the platter,
make sure the box will be large enough to allow plenty of loose fill packing to
protect the platter. This is then stretch filmed in place on the top of
the foam box. Once the foam box is finish packed, it is then suspended inside
the outside box, using loose fill packing (foam
peanuts).
We ship about dozens of tables a year (about 750 units
/ packs
total a year) and have a virtually spotless track record. From the "un-scientific" survey we have done from
customers calling / emailing for parts / insurance claim amounts on units
shipped from amateur sellers / packers, we see an extremely high failure rate on
electronics / tables / reel to reel machines. I have a customer who recently
ordered 10 tables as an experiment
(yes he has a lot of money
to throw around) mostly from all different sellers and he said
of the 10, only 4 came in
essentially undamaged
and given the way they were packed, they should have ALL likely been damaged. Our philosophy is that if something gets damaged in transit, it's almost
ALWAYS
due to inappropriate packaging and not likely the fault of
the shipper / transit company (UPS, FEDEX, USPS etc). Everyone should know
that a package will be dropped, thrown, kicked, subject to thermo nuclear
war etc, so it should be packed to withstand any possible scenario! The worst thing about this is that the world has
lost a lot of really cool vintage gear due to inadequate /
inappropriate packing by sellers who are inexperienced in the proper
procedures, or lack adequate materials to do so. :-(
PS. For years I hear folks preaching that electronics must be
'Double Boxed'. I've even seen that listed on either the FedEx site or UPS's
Site (I don't remember which)..... BS !....In all the years I worked on
the retail floor, un-boxing many thousands of pieces of gear, I can count on
less than one hand the number of times I've seen manufactures 'double box'
anything. You could put something in ten boxes, but if it's not packed inside
the first box correctly, it won't likely matter!
|
MORE INFO AND PHOTOS WILL BE
POSTED
|
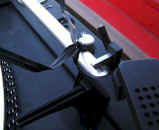
DUAL 500 SERIES TURNTABLE
The tone-arm is then tied in place in it’s “locked” position
with a wire tie on the Dual 500 series.
|
...or held in place with suitable measures such as on the
this B&O Beogram 3000.
|
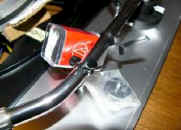
The smaller, lighter weight accessories can be tied
to the tone arm stand / lock as long as they're limited to an ounce or
two. Accessories such as cartridge containers, single play spindles, 45
adapter discs, strung style anti-skate weights (not the counter weight!)
etc.
|
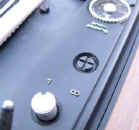
Photo of Dual 500 series above.
Next if there are any transport screws (not as common on single play
turntables as changers, but may still be used) they should be engaged,
which usually means turning them counter-clockwise to their “out”
position. Some single-play tables may have had transport screws, but they
are usually removed for use and subsequently have been lost.
Suitable replacements will need to be acquired. We have an assortment of
any diameter / length we would need on hand.
|
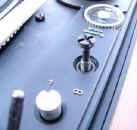
Transports screw in "locked" up position for shipping.
Another version of transport / shipping lock downs;
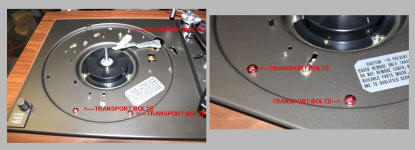
|
Occasionally on belt drive / rim drive turntables the
motor will utilize it's own transport lock bolts. If so, appropriate
bolts will need to be sourced and installed.
|
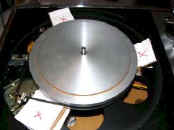
Photo Sansui stereo
turntable SR/4040
Prior to the packing, the table is prepped for packing. If it is a
“single play” type table, the platter is removed. The platter can weigh
anywhere from a pound or two to as much as 10 or 20 lbs. As a “static”
load this may seem like an insignificant amount, but
as a 'dynamic load' as in when being dropped from a
stack of boxes or a delivery truck, a 4 lb platter can pretty easily reach
a weight in motion of 20-80 lbs. Much more weight than the plinth and
spindle / bearing were ever designed to handle. Leaving the platter in
place will generally result in a bent spindle, warped bearing, busted
plinth or a combination of these. A platter left in
place on most turntables will result in damage to the dust cover and the
tone arm assembly from 'flying around freely' inside the now damaged /
ruined dust cover. I have heard of tone-arms completely busted or broken
off from this. We’ll talk about what is done with the
platter and rubber mat later.
(Photo shows internal & integrated platter and not the main
"heavy" platter that has already been removed. In this case
stabilizing shims were added to the internal platter
which was not practical for user to re-install once delivered. If the
smaller platter weighs much more than a half pound or so, then it too
should be removed)
|
|
|
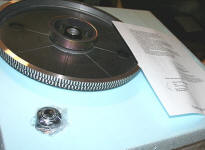
The counter-weight should then
be removed (if
practical) and packed separately. If it can't be
'practically' removed, then it should be held in place by foam. Many styluses and dust-covers are damaged /
destroyed by counter-weights flying around inside that were not secured
or removed. If there is absolutely no way to
remove the counter weight, then it's a good idea to block / restrict
it's movement by sufficient means. We have actually seen the rear tube
of tone arms that have been broken due to a counter weight's mass.
Again, it doesn't seem like much, but when dropped from 3-5 feet, at the
right angle and it can snap the tone arm.
|
|
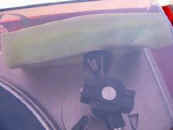
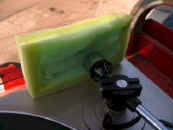
Photo Marantz 6100 series
This was a turntable that arrived to us as a
'trade-in'. While in this case it did arrive intact, and no damage was
done, the counter weight should have been removed and packed separately.
There's no reason on this table not to have done that, and frankly
probably would have been easier than what the person did.
|
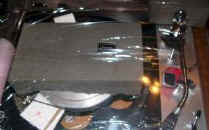
Photo Sansui SR/4040
Stereo Turntable
Foam pad added between dust cover and integrated platter
that was not 'practical to remove' for further
protection.
|
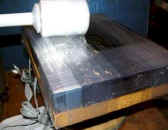
Next the dust-cover is VERY FIRMLY secured in place with shrink film
from every direction. Once sealed down the turntable and dustcover becomes
a solid unit. No motion is allowed. Most turntables
will also have a sheet of 'poly lam' foam between the dust cover and the
plinth to absorb shock. If this technique is utilized (and it should and
usually is), care must be taken to not allow damage to cantilever in
transit or during unpack from the foam sheet.
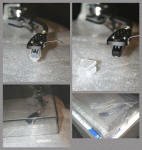
Photo Technics SL-Q2
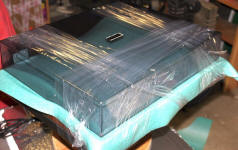
Pioneer PL-55DX dust cover secured w/ 'polylam' foam
to absorb shock
|
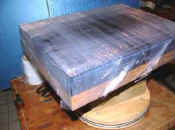
Photo B&O Beogram 3000 Turntable
|
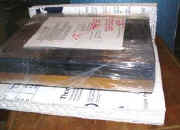
Photo B&O Beogram 3000
Next, our tables are always, housed in a 2" sheet foam
"box" that fits exactly. Once the table is sealed and there are
no parts inside "rattling around" to break things or scratch the
dust cover, it is put into the foam box. On some tables that have
suspension built into the feet, small depressions need to be
"dug" in to the foam where the feet are, so that the tables
weight is not on them for shipping. The internal suspension is not
sufficient for this.
|
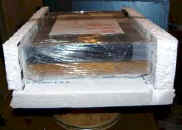
Photo B&O Beogram 3000
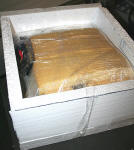
Photo Technics SL-Q2
|
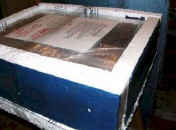
Photo B&O Beogram 3000
|
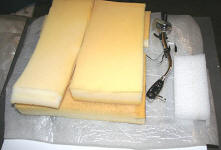
Photo Technics SL-Q2
If there's no dust cover, then
foam must be stacked to protect tone arm.
|
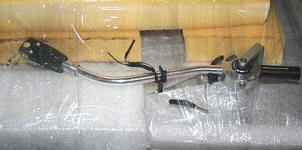
Photo Technics SL-Q2
|
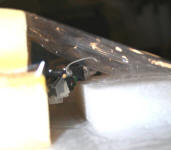
Photo Technics SL-Q2
|
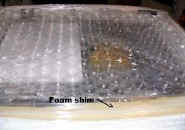
Photo Sansui SR/4040 stereo turntable
Any "play" or space inside the foam box, will be filled with
foam or bubble wrap.
|
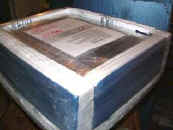
Photo B&O Beogram 3000
A sheet with specific un-packing / re-assembly instructions included with
every table.
|
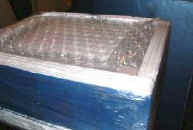
Photo B&O Beogram 3000
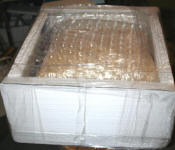
Photo Technics SL-Q2
|
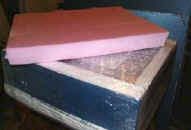
Then a top plate of 2", high-density “pink” foam is sealed
tight to the rest of the foam box with the stretch film. Prior to that if
there's any space between the top of the dustcover and the foam
"lid" that should is also filled to eliminate
up / down movement. We generally use a small sheet
of 1/2" bubble wrap to do that.
|
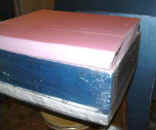
|
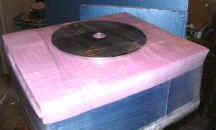
Photo B&O Stereo Turntable Beogram 3000
The platter and rubber mat are stretch filmed to the top of the box
taking care to make sure the mat is not bent or allowed to bend / wrinkle.
The best way to ensure this is to place the mat down first on the box,
then cover it with the platter positioned up-side down, to hold it in
place. This is then stretch filmed in place on the top of the foam box.
|
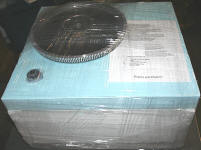
Photo Technics SL-Q2 Stereo Turntable
The platter and rubber mat are stretch filmed to the top of
foam box / housing. Also
present is the counterweight 'dug' into a recess and a sheet containing
all instructions for unpacking, set-up, adjustment and our contact info
for assistance.
|
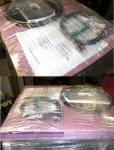
Pioneer PL-55DX ready to place in
final shipping contanier
|
|
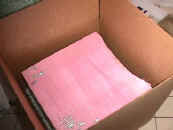
|
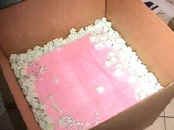
Once the foam box is finish packed, it is then suspended inside the
outer box, using loose fill (foam peanuts). Photo prior to covering the top and sealing the box.
|
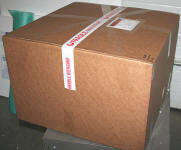
Ready to Ship!
We ship about 50-60 tables a
year (about 750 units / packs total a year) and have
a
virtually spotless track record. On an
interesting side note; I have a customer
/ collector who
recently ordered 10 tables (mostly from all different sellers) and he said
6 came in damaged due to inappropriate packaging.
2 had damage that 'appeared' to be from lack of packing, but could have
existed prior to shipping. 2 fared decently, but by only luck as NONE were
packed appropriately. The worst thing about
this is that the world has lost a lot of really cool vintage gear:-(
|
|
MORE TO COME AS TIME ALLOWS
|
|
Yes, we should all know by now that 'stuff' happens. FedEx or UPS or the
Postman or 'Joes delivery service' will 'drop' packages. There is
simply not enough time for 'carriers' to 'coddle' every package with 'kid gloves' and
accidents happen. They'll fall off conveyer belts, have other packages
fall on them, get 'drop kicked', be used as soccer balls, fall off the
hand truck, fall out of the back of the truck, be involved in
'thermo-nuclear war', etc. They need to be packed so all of that and
more can happen, and still arrive intact and unscathed! If you can't
pack items to that degree, then you probably shouldn't be selling /
dealing in / packing /
shipping them. Sorry, but the world is loosing too much irreplaceable
gear and too many units due to amateurs. If I've offended anyone then
that probably means you.
What qualifies me to to 'be the expert'?
Having unpacked hundreds (maybe even thousands at this point) of electronic units for store
displays, demo's, unpacked and re-packed for tent sales, events, RTV,
customer inspections, etc, not to mention my own use for the past 38+
years of doing this has shown me how the manufacturers do it. Having
shipped ~16,000 units over the past 38+ years, most of which had
to have packaging re-designed / fabricated from scratch, with only 1 or
2 minor damage issues (no, I'm not kidding) pretty much makes me an
expert and the one you should probably be listening to. "Wow, you sound really arrogant!"
I'm OK with that! Sorry, but vintage audio gear, damaged due to inappropriate, inadequate,
unprofessional packing is my biggest 'pet peeve'.
|
LINKS TO OUR 'HI-FI' DEPARTMENTS
Wondering where
the "tone" you remember went?....
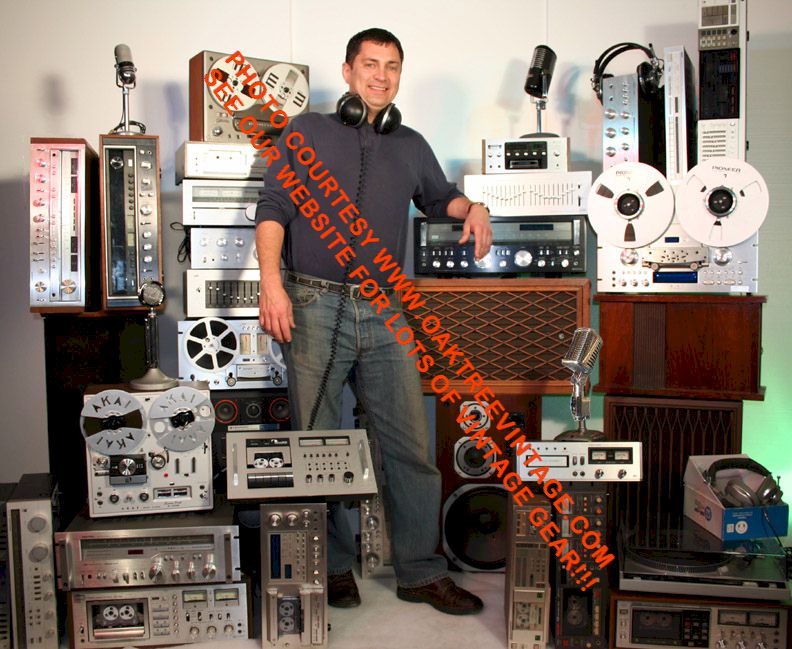
.... Surround yourself with Silver and find it again!
|
- |
-
|
-
|